There are three primary methods of controlling length on a roll former – gauge bars, positive stop, and encoders. The first two methods are completely mechanical, with the last being electro-mechanical.
Recent work has uncovered the mechanism for length control of this self-assembly process. The bacterial flagellum is an organelle that self-assembles outside the cell body. Recent work has uncovered the mechanism for length control of this self-assembly. The easy touchscreen controls and ability to store up to 50 lengths make this a great option for a Gutter or Roof Panel machine. 11.3.5.2 Arc-length Control In an ordinary iteration process the predictions for the displacement increments can become very large. This is the case especially if the load-displacement curve is almost horizontal. If a fixed load increment is prescribed, this results in.
Length Control Methods
- Mechanical
- Length Gauge Bar
- Positive Stop
- Electro-mechanical
- Encoder
Gauge bars and positive stops have been around since the start of flying die applications. They are probably the oldest method of length control for roll forming applications, but they’re still in use today. That’s because they typically offer the best accuracy and consistency for the lowest cost.
Length Control In Endodontics
A gauge bar is just a steel bar pre-cut to the desired part length. It is attached to the exit side of the cutoff, and affixed with a stop at one end to catch the leading edge of the strip as it is driven forward by the roll former through the cutoff die.
When the leading edge of the strip hits the welded stop on the end of the bar, the die is dragged forward by the strip. The base of the cutoff die hits a rocker arm switch that fires the press, and a finished part drops onto a table or conveyor.
In the case of a positive stop, a plate is affixed directly to the rocker arm switch. When the leading edge of the formed part hits the plate, this actuates the switch and causes the press to fire.
Whether you’re using the length gauge bar or a positive stop, you’re physically tying the operation of the cutoff press to the physical length of the finished product. The benefit of this is that the finished part length tends to be very consistent and accurate. The downside to this type of length control is that the process has to stop to handle a length change. Often, there will be at least one scrap part after the change. Production speeds tend to suffer with this type of length control, as well, because if the part profile is very strong, running too fast could rip the stop off. If the part profile is too weak, then hitting the stop can cause the part to buckle and deform. And if you add in-line punching to the mix, it becomes very difficult to synchronize the punch location to the ends of the part.

Mechanical Length Control
Pros
- Consistent
- Inexpensive

Cons
- Lower Production Rates
- More Scrap
- Increased Downtime for Changes
Encoders are used in conjunction with computers to control length. The encoder is often powered from a circuit on the computer, and the data the encoder transmits is fed back to the computer through the same cable that carries the power. The majority of encoders used in roll forming are rotary. The encoder has a shaft that protrudes from one end, which is connected to a measuring wheel with a known circumference.
As the material being formed flows through the machine, it rides across the face of the measuring wheel, causing the wheel to rotate. In turn, the shaft of the encoder rotates and this produces electrical pulses that are transmitted to the computer that controls the machine. The computer has been programmed with the physical length that corresponds to each pulse from the encoder, so the computer accumulates counts to equal the programmed part length. Once the correct length has been counted, the computer fires the cutoff from a solid state output. Assuming a straight line through all punch and cutoff presses, the system can control length for multiple presses with a single encoder and measuring wheel.

The benefit of such a system is that finished part lengths and punch patterns can change on-the-fly, without having to generate scrap between parts. Higher production speeds are also possible, because the act of measuring the part doesn’t have the potential to also damage either the part or the measuring device. The downside of rotary encoders are the measuring wheels. If the wheel is not concentric, or if the bracket that holds the assembly develops backlash, or if the any part of the assembly is misaligned, then length variances can occur. Understanding and performing proper maintenance on the encoder mount is critical to accurate and consistent part lengths.
How Long Is Control
Electro-mechanical Length Control
Control Game Playtime
Pros
- Length and Punch Patterns Changes Occur On-the-fly
- Little to No Scrap on Changes
- Higher Production Rates
Length Control Arm
Cons
- Higher Initial Cost
- Mechanical Backlash and Alignment Require Frequent Attention
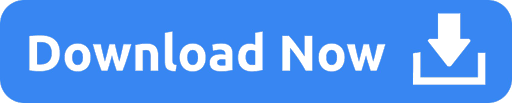